It’s an electrifying time for aviation. Or not, depending on whom you speak to. Proposals and prototypes for electric aircraft range from 18 rotor two seat helicopters, to hybrid powered twin aisle airliners. Between these are re-engined primary trainers, human carrying autonomous quadcopter taxis, and multi-engine general aviation aircraft optimised for fast short-range flight.
These designs are being developed against a background of widely acknowledged climate change, a move toward renewable energy in electricity generation, and the steady growth of hybrid and electric cars.
Yet the hard physical facts of powered flight remain unchanged. Batteries are relatively heavy, yet aircraft are the most weight sensitive of any transportation devices, and even the best currently available batteries have much less energy per kilogram than a litre of liquid fuel.
There’s another reality in play: the requirement for change has already been laid down. The European Union’s Advisory Council for Aviation Research and Innovation in Europe (ACARE) has a target of a 75 per cent reduction in carbon emissions and a 90 per cent reduction of nitrogen oxides emissions by 2050.
In the US, the Continuous Lower Energy, Emissions and Noise (CLEEN) program, has been underway since 2010, a collaboration with industry to develop environmentally friendly aviation technologies. ICAO has had a comprehensive climate change resolution (A38-18) since 2013, that requires member states to develop a global market-based measure to address greenhouse gas emissions from international aviation.
Electrical engineer and specialist in aero-electric power systems, Catherine E. Jones, says these targets ‘cannot be achieved through marginal improvements in turbine technology or aircraft design. Rather, disruptive technologies and more innovative aircraft must be considered,’ she said in a paper presented to the Institute of Electrical and Electronic Engineers (IEEE).
NASA engineer Sean Clarke is the principal investigator for the agency’s X-57, a multi-motor electric experimental aircraft expected to fly next year. ‘We’re at the beginning of a 30–50 year propulsion revolution,’ Clarke told the 2016 Transportation Electrification Conference, near Detroit, in the US.
Electric propulsion would transform aircraft, and, potentially, society, Clarke said. ‘The age of on-demand services is about to lead to on-demand mobility.’
Professor Peter Wilson of the University of Bath says hybrid energy and propulsion systems have become common in marine, rail and automotive transportation. ‘There is an opportunity to use quiet- and low-emission electric propulsion systems in small aircraft, but it requires a high efficiency conventional aircraft engine to provide enough energy for a flight of reasonable utility to be feasible at this stage of battery development,’ he says.
State of charge—current technologies
As the still unfolding field of electric aircraft propulsion is so new, its terminology is still fluid, but four main concepts are emerging. Three of them are propulsion configurations. These are battery electric, hybrid and turboelectric. The other key concept is an aerodynamic innovation, distributed propulsion.
Battery electric. The first battery electric aeroplane flew, admittedly for a mere nine minutes and five seconds, in 1973. Recently, the concept has re-emerged, with more practical performance and range being made possible by the development of lithium ion batteries. The same battery technology has driven the emergence of small drones, in particular electric multicopters. Battery electric aircraft of every size, ranging from single seat short-range autonomously flown ‘air taxis’ to single aisle regional airliners are being developed now, in prototype, proof of concept or concept stage.
‘The fundamental limiting factor in electric aircraft is the batteries’, says senior lecturer in aerospace design and propulsion at the University of Sydney, Dries Verstraete. ‘In battery development, the important trade-off is between power and energy. If you design a battery for high energy you’re typically limited in how much power you can draw and how quickly you can discharge. If you design for a quick discharge, your battery becomes heavier because your electrodes need to become thicker.’
‘You need to choose your battery for whether you want to provide moderate power for a long time or peak power for a short time. It’s not like a tank of liquid fuel that can do both, if required,’ Verstraete says.
One possible solution could be a dual-battery aircraft or one using a combination of battery and fuel cell. ‘It could have one battery for cruise and one for take-off and climb to give you the boost power.’
Associate Professor Martin Veidt of the University of Queensland is a specialist in the development of lightweight materials and structures. He says electric motors are improving in efficiency and output and becoming viable. ‘The magic number has been 5kW per kg of engine weight; then you can start thinking of feasibility studies for aircraft propulsion,’ he says.
However, high output motors bring engineering problems. ‘The big challenge on the mechanical side is how to manage the thermal effects of increased power in electric motors if they are to be used in aircraft propulsion,’ Veidt says. ‘Even though electric motors are very efficient, the less than 10 per cent of wasted energy in a high output motor is enough to create a heat management issue.’
Weight and heat management are competing priorities: in ground-based applications heat is often managed by mounting the motor on a large, heavy, heat sink, a technique which is, to say the least, inelegant for aviation applications. ‘We’re looking at light-weighting and further improving the power density by improving the thermal management and fluid dynamics management of the motor,’ Veidt says. ‘That involves redesigning for reduced weight using novel alloys, composites and innovative manufacturing techniques, such as 3D printing.’
A 2016 report by the US National Academy of Sciences projects that the specific power of motors and generators could increase to approximately 9 kW/kg over the coming 20 years, with power levels of approximately 1-3 MW.
Wilson says, ‘there is a great opportunity for novel materials and design techniques, including additive manufacturing, to design new physical structures for motors, specifically designed to maximise the power to weight ratio, and especially to reduce the unnecessary weight in current motors.’
Hybrid propulsion combines batteries and electric motors (which can also act as generators) with internal combustion engines to get around the range limitations of batteries. Conceptually, they are similar to hybrid cars and fall into two groups: series hybrids, where the internal combustion engine (ICE) acts purely as an electricity generator, and parallel hybrids, which can be powered by the ICE and an electric motor.
Airbus has developed a two-seat hybrid aircraft, the E-fan plus, which it says is ‘a first step in our long-term goals of potentially developing a hybrid-electric regional airliner or helicopter.’
Dr John Olsen of the University of NSW is a research affiliate with the Australian Centre for Space Engineering research. He says battery technology is not good enough for fully electric aircraft at present, but argues that hybrids could be a viable stop-gap. ‘My approach has been to take an internal combustion engine and to downsize it so the engine produces only the power required for cruise. That means the engine will be about 75 per cent of the weight and power of a current engine.’
‘That’s a reasonable downsizing,’ Olsen says. ‘That leaves around 40–50 kgs you can use for something else. My approach has been to fit an electric motor/generator in parallel with the engine. We can then take energy from the batteries in addition to the output of the engine.’
As the weight of the fuel burns off, some of the engine’s energy can be siphoned off to recharge the battery.
Turboelectric systems use a gas turbine in combination with electric propulsion, like hybrids, and like hybrids they can be both series and parallel. Due to the much larger electric currents involved, and the challenges of managing this power, they are emerging as a separate category, particularly in terms of engineering challenges.
Verstraete says, ‘It’s hard to beat a gas turbine in terms of power density, but their problem is that they are much less efficient at small sizes—adequate pressure ratios in small turbines require very high rotor rpm. But for larger aircraft they are an attractive proposition and an efficient foundation for hybrid propulsion,’ he says.
The National Academy of Sciences 2016 report says, ‘Turboelectric propulsion systems are likely the only approach for developing electric propulsion systems for a single-aisle passenger aircraft that is feasible in the time frame (until 2035) considered by this study.’
Energy conversion and transmission losses mean turboelectric systems have lower inherent efficiency than conventional gas turbine propulsion. But the advantage of turboelectric propulsion is how it can be readily adapted to take advantage of aerodynamic efficiency boosters, such as boundary layer ingestion and distributed propulsion.
The report found the combination of turboelectric propulsion, distributed propulsion and boundary-layer ingestion, had the potential to reduce fuel burn ‘up to 20 per cent or more compared to the current state of the art for large commercial aircraft’.
Distributed propulsion reverses the trend in large commercial aircraft towards fewer engines. A distributed propulsion system involves large numbers of electric motors providing thrust and lift. NASA’s X-57 concept aircraft has 14, Volocopter’s electric helicopter prototype has eighteen.
Because electric motors are equally efficient in large and small sizes, using many small ones instead of a few large ones brings unexpected benefits. Redundancy is one. The Volocopter can fly with six of its motors shut down. Wings that are optimised for high-speed cruise flight can be ‘blown’ for low speed take-off and landing lift, as the X-57 does.
‘That’s where the concept of electric propulsion becomes intriguing,’ Veidt says. ‘You can push more air if you have lots of distributed small motors.’
Verstraete says distributed propulsion could eliminate control surfaces in fixed wing aircraft. ‘You could in the long term use a gimballed propulsion system instead of rudder elevator and ailerons, saving the weight of control surfaces and cables. Combined uses are a lot more feasible with electric than with conventional technology,’ he says.
Wilson says the use of wide-band gap semiconductors (such as Silicon Carbide or SiC) in distributed propulsion systems offers great potential in realising robust and extremely efficient power systems for aircraft. ‘Wide band gap power electronics offer the prospect of realistic high power densities in motor drives, power conversion and interfaces to energy storage systems,’ he says. ‘This can potentially make a significant difference to the ability of aircraft designers to design practical electric aircraft.’
Fad or future: The experts’ verdict
One sceptical argument about electric aviation is that the field is merely the latest Silicon Valley fad, a short-term fixation of the technology sector, and an amusing way to burn through a few billion dollars of start-up funding. When the inherent physical and regulatory obstacles become too much these cashed up tech titans will move on, the argument goes.
Engineers with backgrounds in aviation and electrical engineering reject this thinking. Veidt says, ‘I think at the moment there are players coming in with a very solid background and history in electric motor technologies. Companies such as Siemens, Liebherr and Boeing—they are not sponsored by Silicon Valley, not part of its mindset. It’s good to see these historical engineering companies giving it some credibility. There is no guarantee, but with this sort of expertise, I think there’s good potential that this interest will develop into products.’
Verstraete says, ‘the Silicon Valley fad is probably true for some of the more far-fetched ideas—Elon Musk throwing out the idea of the hyperloop, for example, but then again, someone’s just built a working version.’
Verstraete projects electric power will come to general aviation before airline transport. Less stringent certification regulations; fewer issues with scaling up technologies such as electrical power management; and the need for cleaner, more economical new propulsion technologies in GA are factors behind this reasoning. But he thinks general aviation will be a follower, not a leader.
‘For me, the critical thing is what’s happening with cars,’ he says. ‘Electric cars are sort of taking off. They don’t have critical mass yet but they’re getting there. Once that happens, it’s going to trickle down to aviation.’ He acknowledges the differences between automotive and aeronautical engineering but says the trickle down of fundamentally reliable electrical technology, made affordable by an industry that has production runs in the tens of millions, will be a flood of opportunities for light aircraft propulsion.
But he is sceptical about the concept of low altitude short-range flying car air vehicles. Safety would be an immense problem, he says. ‘Personal air vehicles in three dimensions? Look outside at the road. We can’t even do 2D properly. It would require an elaborate and highly reliable sense and avoid network, that would have to be virtually 100 per cent reliable from day one.’
Verstraete does not see a role for human pilots in such a transport system. A system that is reliable and fully autonomous will work ‘because everybody will follow the rules. If some percentage is autonomous and some percentage is human driven, the human is going to break the rules.’
‘I’m all in favour of technology concepts and demonstrators but it’s a big step from those to something practical on a large scale.’
Olsen says, ‘flying taxis? I wonder if they’ve considered the aerodynamics between buildings. It would be a logistical nightmare overseeing traffic of these things. These vehicles are going to have to be in communication with one another and most likely pilotless.’
For larger aircraft, Olsen says a fundamental characteristic of battery power will become a limitation—the fuel weight paradox. ‘With liquid fuels, the weight goes down as the fuel burns off but with batteries, you’re stuck with that weight all the time. For electric aircraft that’s a range-limiter. You have to find extra efficiency to make up for the fact that you don’t lose weight in flight.’
But a city hopper aircraft—737 or A320 sized—would be more viable. ‘We’d have to embed a motor generator in the shaft of the engine. I’d imagine a downsized engine to provide power for cruise and then batteries to supply take-off and climb power.’
Wilson notes that while short-range aircraft for commuter or individual transportation may be feasible, the other issue is charging times. ‘Even if an electric aircraft can be used effectively over short distances, the time to recharge it is significantly longer (often 6–8 hours using current technology) and this would be economically difficult to make practical,’ he says.
‘Despite this obvious stumbling block now, work is being advanced in the area of wireless and rapid-charging systems, which in conjunction with improving battery technology, could lead to viable systems in the medium-term future.’
Verstraete sees a particular conflict between battery technology and the low-cost airline imperative of a quick turnaround—battery charging becomes much less efficient if done rapidly. ‘With foreseeable technology, if you had multiple electric aircraft flying between Sydney and Melbourne and you wanted to recharge them in 30 minutes, you would need a power station at the airport as big as that required to power the entire city,’ he says, looking up from a back-of-envelope calculation.
‘But you can never say never,’ he says. ‘Plenty of famous people have been wrong saying “we’ll never fly”. So while I don’t want to say no, with current technology in batteries, it is highly unlikely that one’s going to happen.’
Veidt is diplomatic. ‘It’s really moving very quickly. Lots of proof-of-concept aircraft will fly in the next 10 years. Then positions will be taken.’ He predicts adoption by 2040s. ‘I think there will be some aircraft in use using some form of electric propulsion but I couldn’t say more than that. I’m an engineer, not a fortune teller.’
Further information
United States Aviation Greenhouse Gas Emissions Reduction plan
Current projects and electric dreams
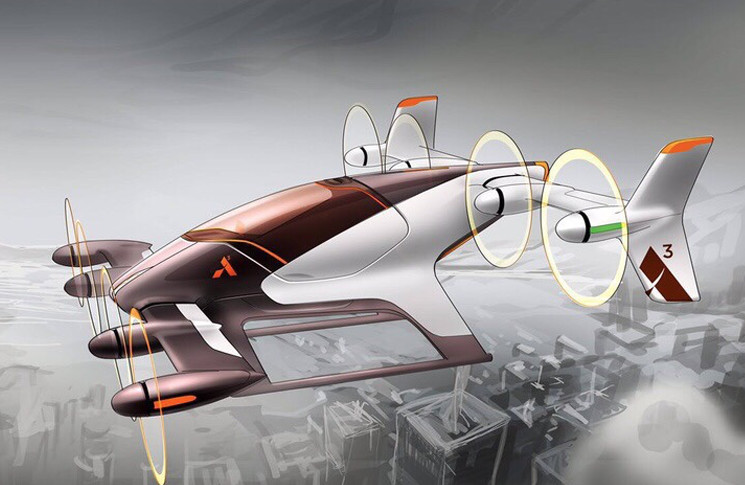
Airbus Vahana
What is it? Vahana is an electric-powered, vertical take-off and landing aircraft with multiple propellers mounted on fore and aft tilting wings. From the website: ‘A core premise of this project is that full automation and sense-and-avoid technology will allow us to achieve higher safety levels by minimising human error while allowing more vehicles to share the sky. Vahana can be an air taxi, but it can also be used as a cargo delivery platform, ambulance, search and rescue, mobile hospital, limousine, or even as a tool to deploy modular infrastructure in disaster sites.’
Who makes it? The Vahana has been developed by Airbus’s Silicon Valley subsidiary A³ (pronounced A cubed). It is ‘a first step in our long-term goals of potentially developing a hybrid-electric regional airliner or helicopter.’
When will it fly? A³ plans to fly a full-scale prototype of an autonomous air taxi by the end of 2017 and plans to fly a production-representative demonstrator by 2020.
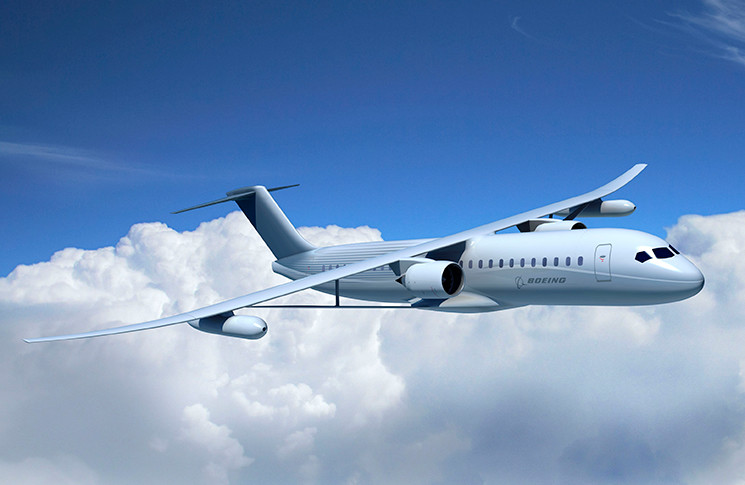
SUGAR Volt
What is it? SUGAR (Subsonic Ultragreen Aircraft Research) is a NASA contract awarded to Boeing for research into subsonic commercial aircraft technology to meet the agency’s future environmental and efficiency goals in the 2030 to 2050 timeframe.
Who makes it? Boeing, in partnership with General Electric, Georgia Tech’s Aerospace Systems Design Laboratory, Virginia Tech and NextGen Aeronautics.
When will it fly? Aircraft yet to be built.
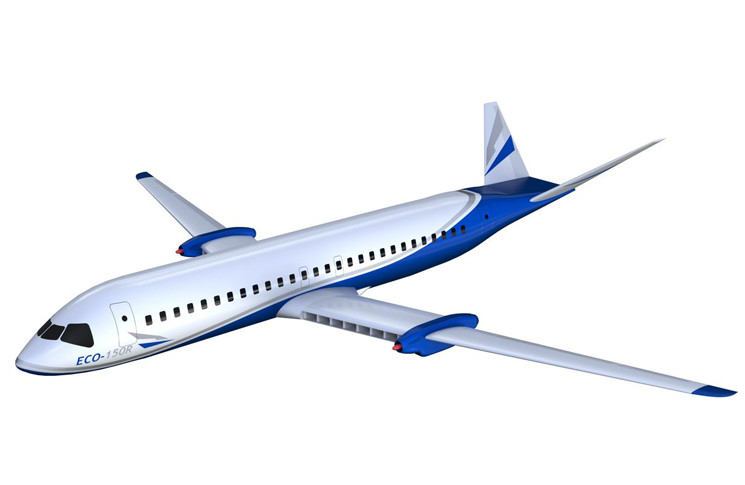
ESAero ECO-150
What is it? The 150-seat ECO-150 has two turboshaft engines mounted mid-span on the wing, driving generators that power an array of 16 ducted fans embedded in the inboard split-wing sections. Fuel savings of 20–30 per cent over the Boeing 737-700 are projected for the conventional-electric ECO-150R version.
Who makes it? Empirical Systems Aerospace (ESAero), Boeing, NASA, Lockheed Martin and drone-maker General Atomics are partners.
When will it fly? Maybe never, but that’s not the point. ESAero describes its projects as ‘vision vehicles which can become research platforms to investigate the potential merits of novel technologies and stand as well defined and reputable reference vehicle benchmarks.’
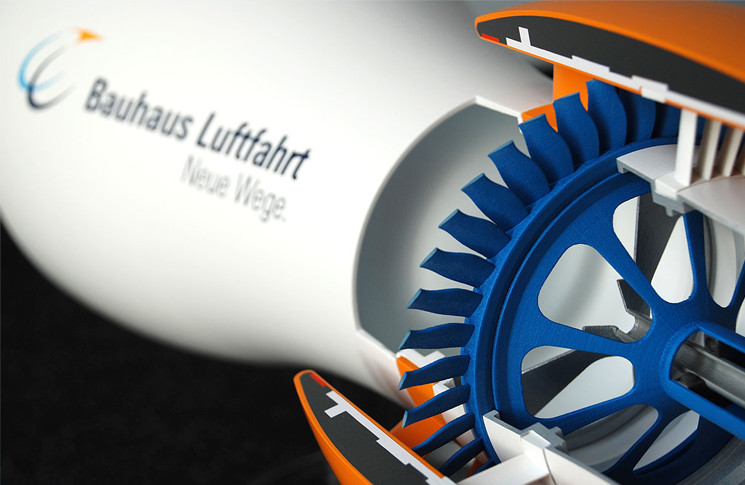
Bauhaus-Luftfahrt
What is it? Bauhaus-Luftfahrt describes itself as a ‘propulsive fuselage concept for an ultra-efficient airliner, with a fan in the tail that ingests air flowing over the fuselage through an annular inlet and re-energises the wake, reducing drag and fuel burn’.
One version has two conventional turbofans under the wings and a third gas turbine in the tail driving the fuselage fan via a gearbox. There’s also a turbo-electric configuration in which generators on the underwing turbofans drive the fuselage fan electrically.
Who makes it? Bauhaus Luftfahrt is a ‘cross-cutting think-tank’ inspired by Germany’s Bauhaus architecture movement. Bauhaus Luftfahrt is a forum for interdisciplinary dialogue between engineers, economists, computer scientists, physicists, chemists, geographers, cultural and social scientists, as well as helping to develop close cooperation between industry, science and politics. Airbus, Liebherr and MTU are partners.
When will it fly? Aircraft yet to be built.
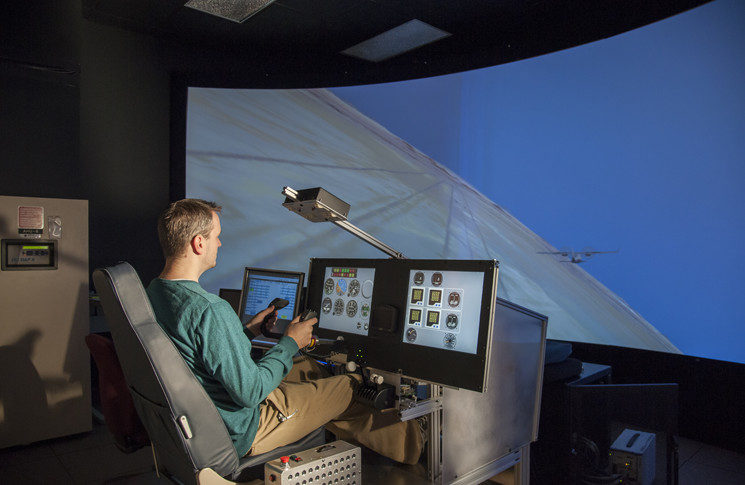
NASA X-57 Maxwell
What is it? A Tecnam P2006T light twin with its wing and two Rotax engines replaced by a high-aspect high-speed wing and 14 electric motors. The goal of the X-57 is to demonstrate a 500 per cent increase in high-speed cruise efficiency, zero in-flight carbon emissions, and flight that is much quieter for the community on the ground.
Who makes it? NASA, with ESAero and Joby Aviation.
When will it fly? Projected first flight has been reported for this year. Wing testing is underway using a ground rig and virtual flights in simulator trials are happening now.
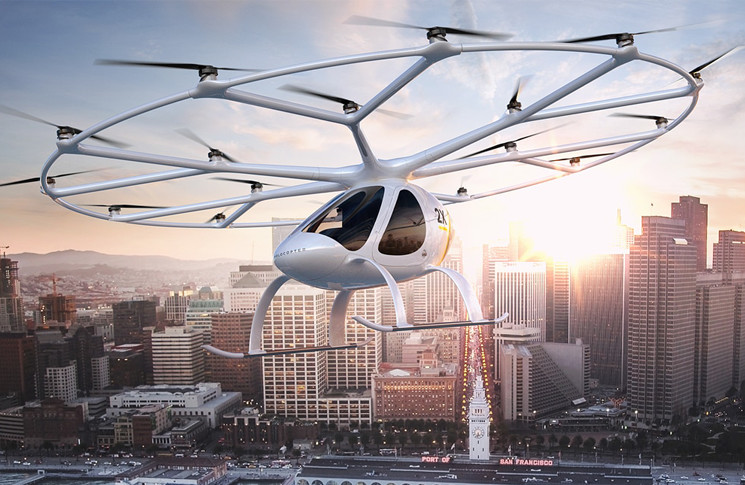
Volocopter 2X
Who makes it? Volocopter, formerly e-Volo, a German start-up company that is pursuing 18-rotor electric helicopter designs.
What is it? A vertical take-off and landing (VTOL) aircraft powered purely by electricity and capable of carrying two passengers. It’s derived from the VC200 prototype and is expected to be offered in piloted and autonomous versions. It has been selected as the vehicle for Dubai’s Autonomous Aerial taxi (AAT) project.
When will it fly? A prototype has already flown. Volocopter says it will deliver vehicles to Dubai in 2018. The German Federal Aviation Office (LBA) will issue multicopter type certification under the new German UL category in 2018.
Won’t happen effectively in the next 2 generations (50yrs). The development costs for a viable mass people mover would be beyond any current Co’s way of thinking. Remember A/C manufacturers are in business to make money with minimal outlay ( they are all struggling as it is with current techno) not to take risks like they used yo do. Aviation has reached its peak only refinements are doable.
In the case of the ECO-150 we are meant to believe that by going from 2 large turbofans that are directly driven, to 16 small EDFs, with the inherently less efficient smaller FSA of these EDFs, and the intrinsic losses in the generators, control circuitry and motors, the overall outcome will result in an marked increase in efficiency. I guess this is some new form of Physics and all the propulsion engineers on the 787’s Trent got it wrong when they went with a 2.8m diameter fan. Whether fixed wing or rotary, you can’t get away from the fact diameter of the fan/prop/rotor has a major influence on propulsion and/or lift efficiency. Therefore, I am continually bemused as to why many of these electric propulsion proposals start with an inherently less efficient planform concept, instead of simply applying electric power to well proven and (comparatively) highly efficient solutions.
Do you notice no one mentions anti icing requirements, power for pressurization and electrical interference from storms, power required for cockpit window heating, power for radar systems, gear and flight control actuation and on it goes. All nonsense. Notice no experienced pilots involved in these discussions
You have to start some where
[…] 4 http://www.flightsafetyaustralia.com/2017/09/watts-happening-behind-the-buzz-about-electric-aircraft… […]
[…] Safran said its innovation teams had been working on hybrid solutions for future propulsion systems for several years. The two companies are the latest to join a global rush to develop electric aircraft. […]