Australian-registered Robinson helicopters have additional stress compared to their overseas counterparts due to their main roles of training, aerial application and flushing semi-domesticated livestock out of the hot savannah country. It is arguable that this places as much of an extra burden on the maintainers as it does on pilots. Experience, along with hard-learnt lessons, have demonstrated that safely operating any Robinson helicopter demands inspections carried out with a level of attention that borders on obsession.
In August 2024, the Australian Transport Safety Bureau (ATSB) issued its report into an accident that took place in February 2022. It had not received much media coverage at the time because nobody was hurt, but it highlighted the importance of focused and informed attention to detail in the maintenance of every Robinson helicopter in service.
‘On 26 February 2022, at around 10:30 local time, a student pilot and instructor were conducting a low-level hover training exercise at the Gold Coast Airport, Queensland, in a Robinson Helicopter R22 Beta,’ the report says.
‘After around 30 seconds of stable hover just above the ground, there was a bang through the airframe. The helicopter then pitched nose up, developed a large vibration and then yawed to the right. The instructor took over immediately and landed. There were no injuries. A subsequent inspection found that the tail rotor gearbox and empennage assembly had separated from the tailcone (boom).’
The accident helicopter had been made in 2006 and had 3,355 airframe hours at the time of the occurrence. Its most recent scheduled 100-hour or annual airframe inspection had been on 24 January 2022 and it had flown 21 hours since.
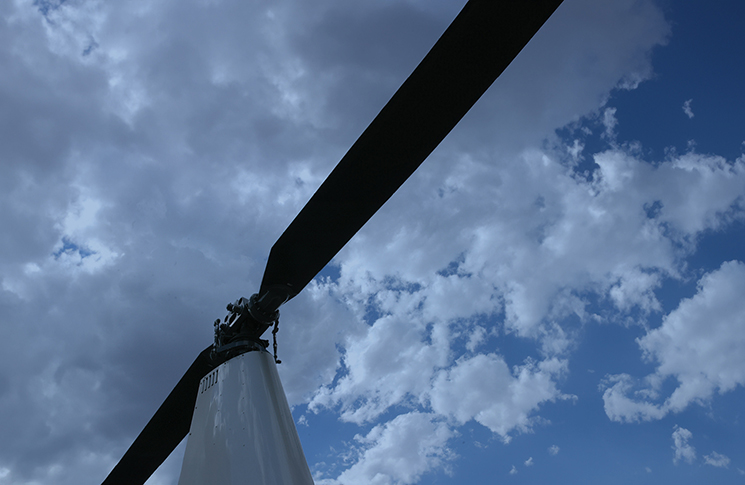
Hours, wear and moisture
The ATSB found a missing tip cap on a rotor blade had caused an out-of-balance condition that led to vibration that wrenched the tail rotor gearbox off the helicopter tail boom. It sent the blades to the US for inspection by Robinson in conjunction with the US National Transportation Safety Board. It concluded that the tip cap had detached from the blade as a result of moisture-induced adhesive failure. The chemical bond holding the metal tip to the composite blade had broken and under centrifugal force at the end of the blade, the tip had flown off. The unbalanced tail rotor overstressed its gearbox and mounts almost at once.
The tail rotor blades fitted to the helicopter had a 2,200-hour operational or 12-year calendar life limit. They were installed as a set in November 2018, having accrued 1,155 hours on another helicopter. At the time of the occurrence the blades had 2,147 hours since new (53 hours of life remaining) and had a calendar life expiry of April 2028.
The tail rotor blades had been repainted in November 2020. But by February 2022, this coat had been worn from the outer leading edges which showed subtle corrosion and pitting. Keeping the tail rotor blades painted was a recommended practice in the R22 maintenance manual, which said ‘maintaining the paint finish will reduce corrosion and erosion.’
Robinson Service Letter 93 of June 2021 said, ‘Paint offers the best protection against leading edge corrosion’ and the ‘preferred blade condition is with a fully painted leading edge’. But there was no specific limit or requirement in the manual or service letter for repainting due to general wear.
Both blades had small areas of corrosion which was indicated by paint bubbles on the blade skin adjacent to the tip cap. The other blade also showed signs of adhesive failure at the tip cap.
Pre and post: what worked and what didn’t
Analysing this accident through the lens of defences and mitigators is valuable because these concepts help identify factors that either lower the risk of the accident happening or, if it does occur, lessen its impact. Some worked well, some did not.
A subsequent inspection found that the tail rotor gearbox and empennage assembly had separated from the tailcone (boom).
PRE – inspection and precaution
The tap test
The helicopter had been through its most recent scheduled inspection 21 hours before the accident flight. This inspection involved testing the rotor blades using one of the oldest techniques in engineering – tap testing. Tap testing predates aviation by about 60 years and was first employed as a means of detecting cracks in railway wheels. A cracked train wheel sounds dull when struck with a hammer and the same is true of a failed adhesive bond in a helicopter rotor blade: when tapped with a coin it will sound ‘hollow’.
Tap testing is as much of an art as it is science, and doing it reliably requires experience and frequent practice. Internet video, including Robinson Helicopter Company’s own video guide, is a valuable teaching aid but does not substitute for experience, a sound ear and an appropriately suspicious mind.
The ATSB report said, ‘Tap testing of the tail rotor blades during the recent scheduled inspection, for the purpose of detecting adhesive failure, did not identify any debonding that were very likely present at the time.’
Failure to detect does not imply the tap test was done poorly. Tap testing can be fooled by unbonded parts still in tight contact. ‘Unbonded substrates maintaining good contact with the adhesive or, as in this case, bonds with extensive adhesive failure, may not produce a clear acoustic difference,’ the report says.
The daily check
Before the first flight of the day, the instructor had inspected the entire aircraft including its tail rotor. Again, there is no reason to think this check was done anything less than competently, but it failed to discover the debonding that brought the helicopter down.
A post-crash inspection found the blade that had lost its tip cap had a crack in the leading edge, across the tip cap bond. The heavily oxidised condition of the crack surface indicated that it was not a recent fracture and, therefore, pre-dated the tip cap separation. However, the ATSB noted ‘It wasn’t possible to establish how the crack would have initially presented and whether it would have been readily identifiable under unaided visual inspection.’ The gradual-followed-by-sudden nature of crack propagation means it may well be invisible to the naked eye until seconds before the blade debonded.
The operating procedures
The day’s lesson was in low hovering. This was done at a height of 5 feet or less and placed the helicopter in the safe area of the height-velocity curve. The taxi to the training area had also been done in this safe zone. It placed the instructor and student in the best position to handle what happened next.
After the bang
The instructor immediately took control of the helicopter, lowered the collective and closed the throttle to control the yaw. This was a drilled and quickly carried out action, enabled by thorough frequent training and the instinctive situational awareness that comes from the combination of training and experience.
Recovery from tail rotor failure in forward flight is possible because in autorotation there is no torque load on the main rotor, therefore, no need for a tail rotor. In practice it is a manoeuvre that can become the most memorable few seconds of a helicopter pilot’s career regardless of the result.
In this accident the problem developed without warning, but procedures and training mitigated its effects and engineering measures were put in place to make it less likely to happen again.
POST – engineering response
Robinson released updated service bulletins and service letters. Revision A of R22 service letter 93 in June 2022 required blade replacement with any evidence of bond line corrosion. The updated service letter required inspection of the bond line with a 10x or greater magnifier to increase the likelihood of detection.
On 22 December 2022, Robinson published revision A of R22 service bulletin 120, R44 service bulletin 112 and R66 service bulletin 41. These listed blade part and serial numbers that had been deemed susceptible to corrosion. Additionally, a new recurrent visual inspection was to be inserted into the pilot’s operating handbook and carried out before the first flight of the day. Any indications of corrosion or exposure at or next to the tip cap bond line required compliance with service letter 93 before further flight. The susceptible blades were required to be replaced no later than 31 December 2024 or as soon as practicable in helicopters operated near salt water.
Robinson made newer revision blades with tip caps manufactured from a different alloy to reduce the likelihood of corrosion.