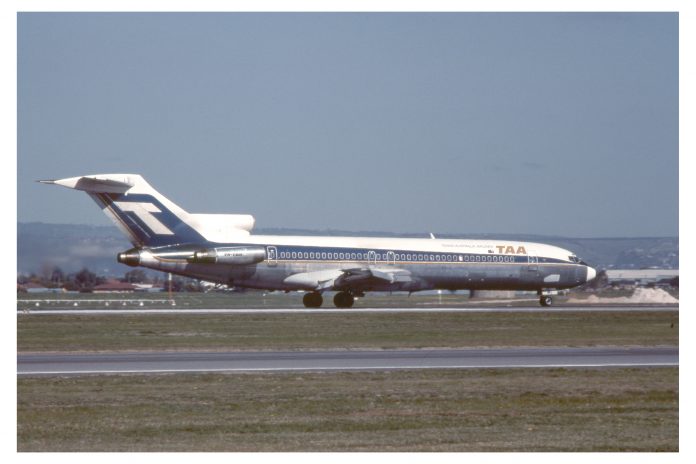
A young engineer who followed his training and stood his ground when others assured him there was no problem may well have saved his airline from disaster, in this close call first published in May-June 2010.
Name withheld by request
In the mid 1980s I worked in line maintenance for a large, great Australian airline, sadly now gone.
During this time I worked with some great fellows on a tight-knit maintenance crew. The age and experience of this crews members varied from LAMEs and AMEs that had been in the industry since the days of Australian National Airways right up to recent ex apprentices including some who were the sons of current and former airline workers plus a good spread of LAMEs of various backgrounds and experience. It mixed in a nice balance of youth and experience. I was a LAME and as a recent refugee from competing airline, I had been made to feel welcome in this crew. I enjoyed my time with this eclectic group.
On a pleasant late spring Saturday afternoon our line maintenance crew happened to be rostered for duty on a 14.30 to 22.30 afternoon shift. Afternoon shift meant that the whole crew would be on the tarmac at the company’s passenger terminal doing turnarounds and maintenance activities on company and customer aircraft.
Although I do recall thinking that the weather was so nice that day that it would have been ideal afternoon to be at home with the family or at a barbecue with friends, but if you must go to work on the weekend and in the great outdoors then the days didn’t come much nicer than this; warm soft sunshine and a gentle breeze.
This company’s flying activities on Saturdays were always somewhat quieter that during the other days of the week. This meant that some of our line maintenance crew would be looking after the needs of transiting aircraft, whilst others of the crew would focus on deferred maintenance that was outstanding on aircraft that had finished their day’s flying and were parked at various gates on tarmac at Melbourne airport.
One such aircraft was a company Boeing 727 that had been parked at a standoff bay.A young LAME was assigned to check the aircraft over and ‘put it to bed’. This included an external visual check of the aircraft and its systems.
This young man had joined our crew only in recent months he was a keen well-liked ex-apprentice who had previously spent a lot of time in the aircraft overhaul department working on and getting to intricately know the inner workings of Boeing 727. He was enthusiastic and had a particular like of the type.
During his end of the day flying check he discovered that one of the 4 main landing gear brake assemblies was worn to limits and this would require changing before the next day’s flying.
The 727 brake unit is a line replaceable unit and although its replacement would normally be scheduled to be carried out when the aircraft was positioned in the hangar, it was a task that could be carried out on the tarmac and it would be no real chore to do it in the open on such a nice afternoon.
The 727 brake unit is a large and heavy multi-disc assembly that fits co-axially over the landing gear axle and the main landing gear wheel and tyre assembly fits over and engages with it. Unlike general aviation aircraft the brake unit is not relined with friction material, but rather the whole module is changed as a complete assembly. This module is fastened to the landing gear with a dozen or so nuts that are tightened on to large studs that project from the main landing gear brake housing through corresponding mating holes in the aircraft’s landing gear axle flange.
As a fast heavy aircraft like the 727 generates a lot of heat and dissipates a lot of energy through its wheel brakes. It was a mandatory company requirement to not reuse the main landing gear brake retaining nuts when a brake assembly was replaced, but to replace them with new ones.
When our young maintenance worker travelled to the company parts store and ordered a serviceable 727 brake assembly he diligently ordered a packet of new brake retaining nuts.
When he received the brake unit retaining nuts from the storeman, they were correctly packaged in a vendor’s bag which identified the parts as the items he had ordered and the package was also supplied as required with a general release note (GRN) number.
On closer inspection, the nuts he had just ordered appeared identical to the ones he had removed and while they were clearly new parts, each new nut in this packet had a small innocuous dot of red dye on it.
Although they had come supplied with a GRN -which is normally proof that maintenance workers can rely upon to indentify serviceable aircraft parts, with acceptable history and traceability – our young LAME was troubled by the red dye stains. He knew from his time in the company component overhaul department that when aircraft parts were determined to be beyond repair and scrapped it was normal practise to mark them with red paint as a visual cue of their soon-to-be-discarded status.
He decided to confer with some older hands on the shift about the conundrum he faced. He was assured by all the maintenance crewmembers present including me that if the parts were the correct part number and as they had been supplied with a GRN then he could rely on them to be serviceable parts and he should use them.
Our young worker wasn’t convinced by the assurances of his more senior peers and as events unfolded it was good that he wasn’t.
He decided to order more nuts from the store to see if he could get a set that were not marked with any red dye. As this airline was a large operator of 727s they had good stock of these parts and he managed to find a set of new fastening nuts that were unmarked with red dye. He then quarantined the nuts that had dye marks for the quality assurance (QA) department attention and submitted a report that asked them to follow up his concerns.
Some weeks later our young LAME, rather proudly and with more than a hint of gloating to his more experienced peers ,announced to the crew room that he had been correct about the brake nuts. He went on to explain that QA had investigated the matter and they had discovered that although the parts came from a reputable and trustworthy vendor that the airline had used for years they were counterfeit.
Further, QA investigations had discovered that the nuts were made by a reputable overseas aircraft fastener manufacturer with all the correct part manufacturing approvals. However, during the post production quality testing they had been rejected as below the required Rockwell hardness value and sent to be scrapped – hence the red dye marks.
At around this time it was believed that person or persons unknown had taken these rejected parts, forged the paperwork and sold them back into the aircraft parts supply chain in the USA, from which they eventually ended up in our young LAME’s hands.
His discovery prompted a company-wide alert to check other 727s with recent brake changes to ensure they didn’t have any red-dyed nuts installed. There was also a worldwide alert to 727 operators advising other operators who may have purchased these nuts from the same supplier.
Fortunately, this episode did not result in any thing more than some light hearted teasing of the more experienced members of the maintenance crew, but it was a telling reminder that maintenance workers must always be vigilant for evidence of bogus aircraft parts and to always follow their instincts if things don’t seem right.
The morals are:
- If it doesn’t seem right or feel right just don’t accept it at face value. It pays to check it out.
- You can teach old dogs new tricks.
- And thirdly just because some workers are young and relatively inexperienced it doesn’t mean that they cannot bring a new perspective.
Interesting read, hate to imagine what has slipped thru over the years though? When humans are involved corruption is ever present!
I pays to be Vigilant…
Counterfeit parts can and do cost too much damage, as well as loss of life.