A tiny, inexpensive part was ignored for decades until it failed, with dreadful consequences.
The fiery crash of a 44-year-old Mooney MJ201 in 2022 remains a stark reminder to engineers and operators that ‘on-condition’ maintenance does not mean ‘fit and forget’ or ‘fit until failure’.
Witnesses on the ground said the first sign that something was wrong with the aircraft was the smoke and flames trailing behind as it descended at Luskintyre Airfield in the NSW Hunter region.
The pilot had broadcast his intent to return to nearby Maitland Airport after his early afternoon flight.
Instead, a dangerous change in circumstances prompted him to make an emergency descent in a desperate attempt to land on Luskintyre’s runway 30.
Apparently affected by heat and smoke, he landed short and slammed into a row of trees about 330 metres before the runway, resulting in what witnesses described as an explosion and accompanying fireball.
The single-engine aircraft broke up and the fuselage was engulfed by an intense post-impact fire.
The pilot initially survived and was found about 10 metres from the burning aircraft. He was able to tell witnesses there had been an engine fire and he had suffered smoke inhalation. He survived for 10 weeks before succumbing to the serious burns received during the crash.
The Australian Transport Safety Bureau (ATSB) said fuel released and atomised as the wings separated from the fuselage, had likely been ignited by the pre-existing fire within the engine compartment.
But it was what had caused the initial fire that worried investigators.
They found that the O-ring fitted to the outlet fitting of the engine-driven fuel pump had likely been in place for more than 29 years without being disturbed.
The O-ring had deteriorated with age – with evidence of loss of pliability, permanent deformation and surface defects – and was no longer providing an effective seal. This allowed fuel to escape and ignite a fire in the engine compartment.
The four-cylinder Lycoming engine had been installed in this airframe in 2021, prior to a sale by its former owner, and an engine condition report accompanying a 100-hour inspection had not identified any faults.
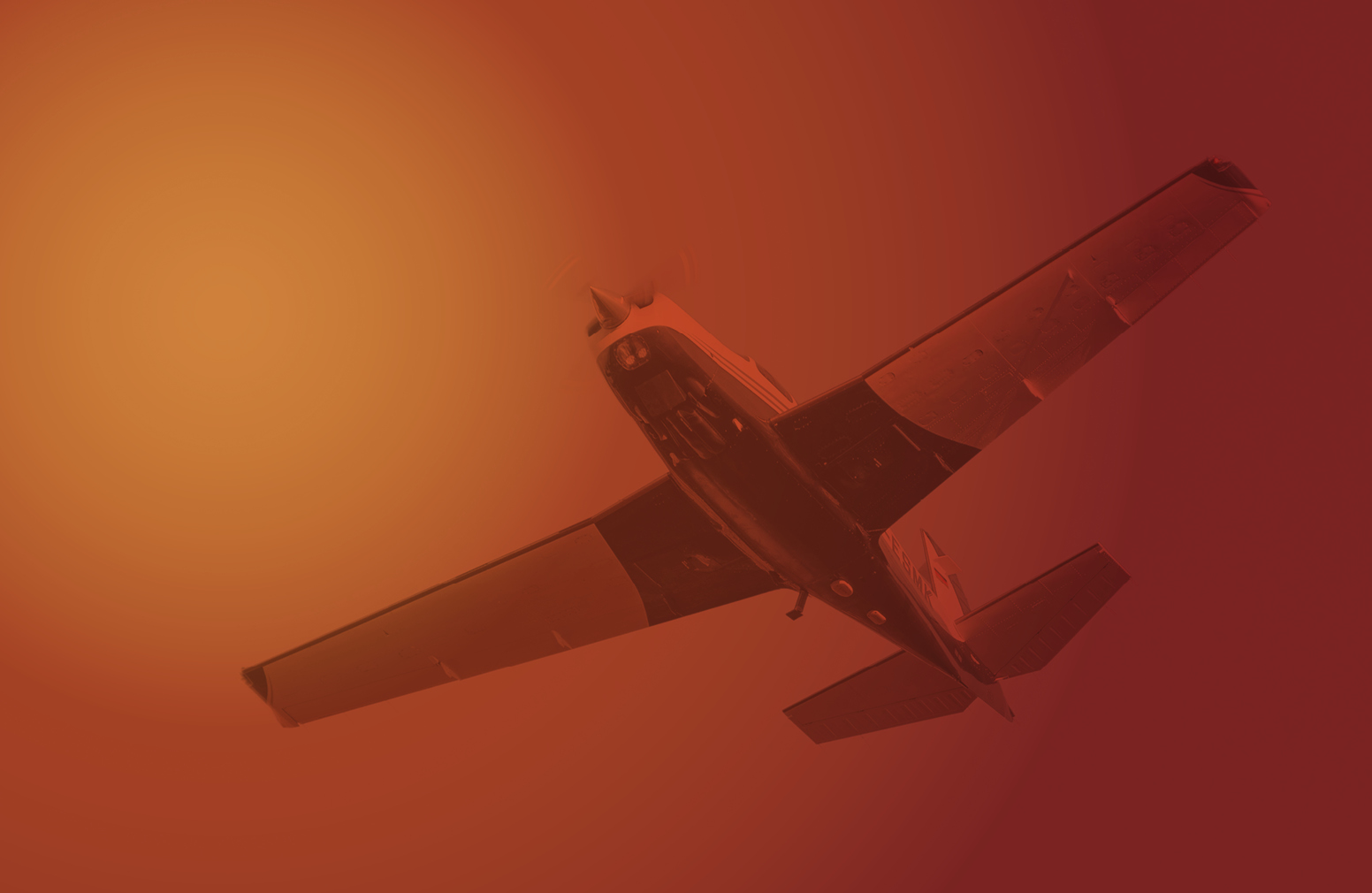
The engine had accumulated just over 1,806 hours but it had not been overhauled since May 1993, almost 3 decades before the accident.
The ATSB noted that the engine manufacturer recommended the engine type was to be overhauled on accumulating 2,000 hours’ time in service or every 12 years.
Continued operation beyond 12 years was allowed, provided continuing airworthiness requirements for on-condition operation were met. However, there was no indication in the available aircraft records that the engine-driven fuel pump had been replaced or repaired.
‘Unlike the engine fluid carrying hoses that were periodically replaced per the aircraft’s maintenance schedule, the fuel pump and the O-ring seals were on-condition and had not required replacement while the engine was in service,’ investigators said.
‘Additionally, the maintenance records did not contain evidence of other opportunities to access and physically examine the condition of the O-ring seals that are normally hidden from view when installed on the fuel pump fittings.’
With the O-rings overlooked for proactive replacement, investigators said assuring the seals were functional relied on checking for fuel leaks at specific intervals.
‘When last inspected, it was likely that no discernible leak was detected at the fuel pump outlet fitting,’ they said.
‘However, the engine was about 17.5 years past its normal overhaul calendar life and the potential for a leak to develop between scheduled inspection intervals was increasingly likely as the O-ring seals continued to age.’
The accident prompted the ATSB to issue a safety advisory notice urging piston aircraft operators and maintainers to proactively replace O-ring in fluid-carrying systems before they naturally deteriorate with age.
‘Inspect the uninspected,’ ATSB Chief Commissioner Angus Mitchell said in releasing the report.
‘If aircraft records identify elastomer – rubber-based – type components that have remained undisturbed for significant periods of time, take a proactive approach – replace components such as O-ring seals before they deteriorate to the point of failure.’
It’s a message also emphasised by CASA in an updated airworthiness bulletin issued in response to the tragedy. The document, AWB 02-001, reminds industry how ‘on-condition maintenance’ should work and the philosophy behind it.
The primary message is that on-condition maintenance is not ‘fit and forget’ or a case of doing nothing until a failure occurs.
It warns that doing nothing could result in nasty surprises which could prove costly or, worse, jeopardise the safety of an aircraft and its occupants.
“On-condition maintenance is not ‘fit and forget’ or a case of doing nothing until a failure occurs.
Heeding the warnings
On-condition maintenance is based on the premise that aircraft mechanical components do not fail abruptly but give some warning or sign they are about to break.
It applies to components whose continued airworthiness can be assured through means such as a visual inspection, measurement or other tests, without the need for them to be disassembled or removed.
Determining the upper or lower limit of a parameter such as fluid pressure or monitoring the solids content in a lubricant could, for example, give an indication of the amount of wear on a component.
With an O-ring, an engine power run and leak checks could determine whether the part is working as well asit should.
The idea is that appropriately timed checks will give you enough warning to allow an item to be removed before that costly or potentially fatal in-service failure.
The on-condition regime is an alternative to ‘hard time’ maintenance where items are replaced or overhauled after a set period of time, usually referred to as time between overhaul (TBO).
Its efficacy has been backed by data indicating up to 89% of commercial aviation components can benefit from on-condition maintenance.
CASA Maintenance Specialist Engineer Indy Weerasinghe says on-condition maintenance offers operators a smart way to reduce costs.
Done correctly, it’s cheaper to inspect an item than blindly replace it irrespective of condition, he says.
‘The concept of on-condition maintenance has been around for decades and is a proven,
cost-effective maintenance philosophy, if it’s understood and done correctly,’ he says.
‘But there is a misunderstanding sometimes that on-condition maintenance is a case of, “If it hasn’t failed, she’s good to go” and that’s incorrect.
‘And that seems to be, at least on the face of it, what happened with this particular aircraft in terms of the O-ring.’
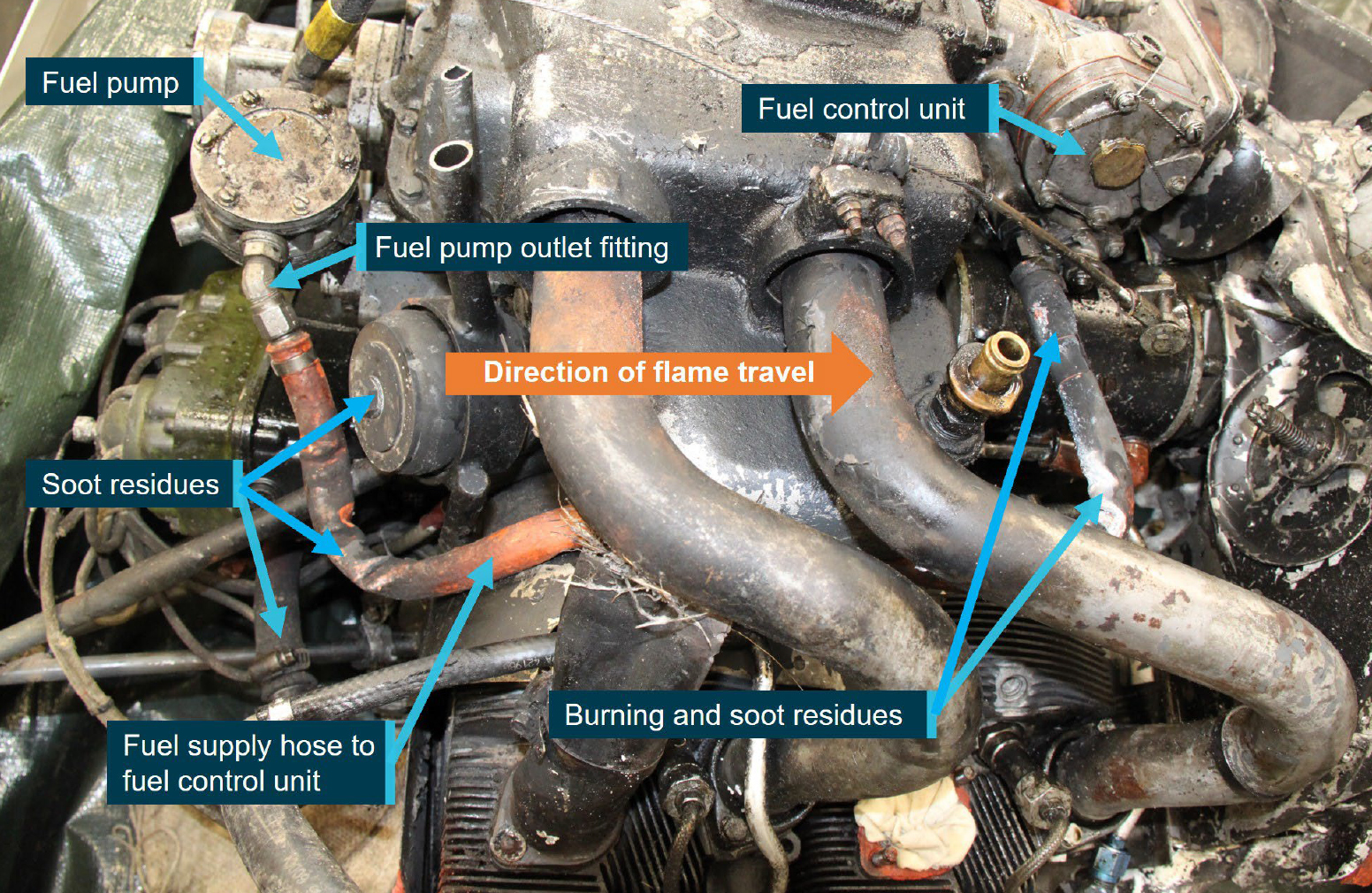
The surprising conclusion that many components do not benefit from a set limit on operating age was first raised in an analysis across commercial aviation in the 1960s that would lead to the development of a concept called reliability-centred maintenance (RCM).
In 1968, with the introduction of the Boeing 747, an analysis method was adopted known as Maintenance Steering Group 1 (MSG-1) with the aim of achieving increased efficiency by avoiding unnecessary maintenance tasks.
This was so successful that it was widened to MSG-2 in the 1970s for other air transport aircraft as a process-oriented system that introduced the concepts of condition monitoring and on-condition maintenance.
MSG-2 was reborn in the 1980s as MSG-3 and has been running in various iterations since. While MSG-2 was process oriented, MSG-3 identifies the consequences of a failure and suggests tasks to mitigate those consequences. This includes providing methods and flow charts which could be used to develop maintenance strategies.
National aviation authorities have input into MSG-3 – CASA is one of 11 regulators who sit on a policy board that looks at improvements that are typically suggested by industry.
Although used mainly by air transport manufacturers, companies such as Textron are increasingly opting to use MSG-3 for smaller aircraft.
‘MSG- 3 is the gold standard for all of this analysis – in effect, it is mandatory for transport category aircraft above a certain weight limit,’ Weerasinghe says.
‘But the engineering philosophy is still applicable to the small end of town. At the end of the day, a fuel pump’s a fuel pump – the way it behaves and degrades is still the same.
‘With the idea of on-condition maintenance on O-rings, the fundamentals are equally applicable, whether you’re talking an Airbus or a Boeing or a Cessna.’
Timing is everything
A major question is: how often, and when, should inspections take place?
A concept to emerge from RCM research is to look at the interval between a potential failure, designated as P, and functional failure, designated by F.
This ‘P-F interval’ assumes a component starts out in good condition and then gradually deteriorates over time and, at some point, can be detected by whatever inspection method is being used.
If the component is left untouched, it will eventually fail.
Weerasinghe says regular inspections should be made between the first point some degradation can be seen and the point where it is likely to fail.
He points to a garden weeding scenario shared by a former CASA colleague as a good analogy.
‘As the weeds come up, initially you can’t really tell them apart from the grass,’ he says.
‘But at a certain point, it grows enough for you to be able to look at it and identify it as a weed. That’s your P, the initial point at which you can detect that it is a weed.
‘If you let it keep growing, it reaches a certain point where the seeds mature and disperse. That can be your F – it’s too late then.
“If the component is left untouched, it will eventually fail.
‘So you need to have an inspection interval between those 2 points where you’re visually able to say that’s a weed and pull it out before it hits that point where it seeds and disperses.’
To reliably detect potential failures and prevent an actual failure, a rule of thumb is that inspections should be made at about one half of the P-F interval.
‘As long as you’re no more than halfway in that P-F interval, the inspection is timed at an effective interval,’ Weerasinghe says.
‘Doing it too early means you’re just adding labour costs for an unnecessary inspection.
‘There might be some performance degradation but it’s not enough for you to be able to effectively detect it.’
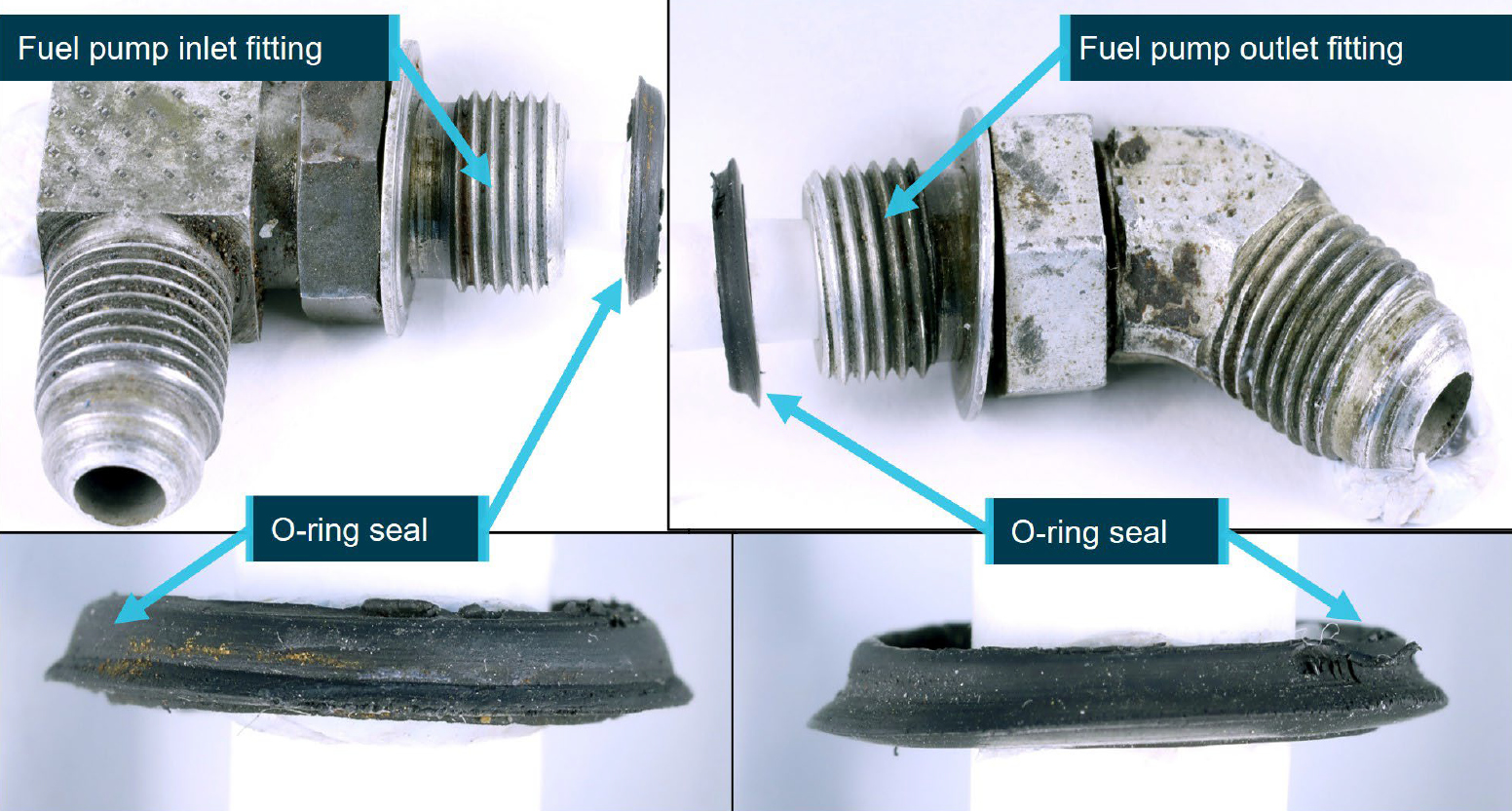
While components which meet documented standards can remain in service, Weerasinghe says the message that on-condition maintenance is not a philosophy of fitting components and forgetting about them until they fail cannot be emphasised too strongly.
Checks that could detect when a component is starting to degrade need to be made, particularly for those parts whose time in service is approaching a manufacturer’s recommended TBO.
Aircraft engineers, operators and pilots should be aware of this message, he says.
‘I think for the smaller end of town, it’s good to make owners who are probably pilots of their aircraft, aware of this so they can have discussions with whoever they employ or contract to do their maintenance,’ he says.