Michelangelo were alive today, he might not be bothered with a hammer, chisel and block of stone. In the Renaissance, the only way for an artistic genius to create a masterpiece of sculpture was to chisel away at unyielding raw material. That was subtractive manufacturing – start with a block of marble, finish with a statue of David.
Additive manufacturing is the opposite, making the statue – or, more relevantly for aviation, the component or component assembly – out of many tiny pieces of material. A Lego statue of David could technically be called a piece of additive manufacturing (putting aside questions of artistic merit) but in the 21st century, the process of joining materials to make objects from three dimensional model data has grown in sophistication, scope and potential.
What used to be called 3D printing is now a suite of manufacturing techniques delivering unprecedented advantages in performance and cost while promising gains in safety. And it’s here now: if you have recently had a dental crown fitted over a decayed tooth, you probably have a piece of additive manufacturing in your head.
Additive manufacturing means it takes the same effort to produce a complex shape as a simple one. This ‘complexity for free’ makes it possible to improve the designs of many conventionally made parts and assemblies. Weight reductions of 30-40% are typical when going from a welded or cast aluminium assembly to an additively manufactured one. Strength can be increased simultaneously with material removed in the computer-aided design process from low-stress areas and added to high-stress areas.
Additive manufacturing does not require the same economies of scale as conventional manufacturing. Its digital and decentralised nature is compatible with local production and small product runs (no jigs or tooling need be changed) and also allows rapid prototyping and responsive design iterations. It reduces wastage of expensive materials.
Science Direct reports the additive manufacturing market has experienced significant growth, projecting a compound annual growth rate (CAGR) of 18.2% until 2026. The global additive manufacturing market is forecast to reach approximately US$76.20 billion by 2030, with an expected CAGR of 20.9% from 2022 to 2030.
The additive ecosystem
Additive manufacturing for the fuel nozzles of General Electric’s LEAP engines resulted in a fuel nozzle that weighs 25% less and is made up of fewer subparts, requiring less resources for assembly. The GE Catalyst engine that will power the new Cessna Denali aircraft has more than 30% of its components made using additive technology, providing benefits for efficiency and weight. The GE9X engine that will be flown on the Boeing 777X has 228 additive manufactured components that weigh 30% less then conventionally produced versions and contribute to a 10% efficiency improvement over previous versions of the engine.
‘Most rocket engines leaving the planet these days are additively manufactured,’ Bruce McLean, chief engineer at the University of Sydney’s manufacturing hub, says. ‘You can literally print a 20,000-pound thrust engine that you can comfortably hold in two hands.’
Additive manufacturing can replace entire assemblies with single parts. Additive Manufacturing magazine describes its advantages in replacing the labour-intensive processes required to produce and validate components made from composites. The trade magazine says efficient use of raw materials can make additively made titanium components potentially less expensive than aluminium ones, once the costs of heat-treating aluminium are taken into account.
However, the magazine cautioned that the true cost of an additively manufactured (AM) part included more than the simple cost of making it. ‘The price of a production-ready AM part is in its ecosystem cost,’ it says. ‘That is, the cost of making it, plus all the costs around this related to sourcing, handling, shipping and inspection. The ecosystem cost is the only way to accurately answer the question, “What will this AM part cost us versus making it the conventional way?”’
Additive manufacturing means it takes the same effort to produce a complex shape as a simple one.
Novelty, opportunity and challenges
Boeing’s vice-president of additive manufacturing Melissa Orme says additive manufacturing is starting to change engineering culture but warns the transition must be safety focused.
‘By culture, I refer to the “additive-first” mindset when engineers embark upon a new product design,’ Orme told the 2021 Rapid + TCT conference in Chicago. ‘The transition to this cultural mindset is necessary to achieve the full benefit of additive manufacturing when inserting onto new products. As a community we cannot simply demand this cultural transformation; rather it must be earned through a deep understanding of the science of AM and through the creation of databases that demonstrate repeatable and reliable performance.’
Repeatability is also a concern for CASA and other national aviation authorities. Safety requires every component used on an aircraft meets its design specifications for areas including strength, fatigue, corrosion resistance and flammability resistance.
The key word is repeatability, CASA Principal Certification Engineer Darryl Taylor says.
‘That means getting a consistent level of strength and flammability resistance and being assured the technology isn’t introducing variability,’ he says. ‘We are short of the data we need to progress in the same way as we can for conventional techniques.’
CASA Manufacturing Inspector Adam Williams says the challenge is control of the variables in the process.
‘We have long established consensus standards for material properties for alloys and composites, whereas for additive manufacturing, there aren’t any established consensus standards at the moment,’ he says. The novelty of AM means a lot of ‘homework’ must be done to establish standards to ensure consistency and repeatability, he says.
Taylor agrees that drones could be the appropriate aircraft to test and validate additively manufactured components. ‘They don’t have to be certified, carry no people and are not allowed to fly over populated areas.’ He expects data from civil and military drone operations will inform the development of standards for crewed aviation.
Additive manufacturing can replace entire assemblies with single parts.
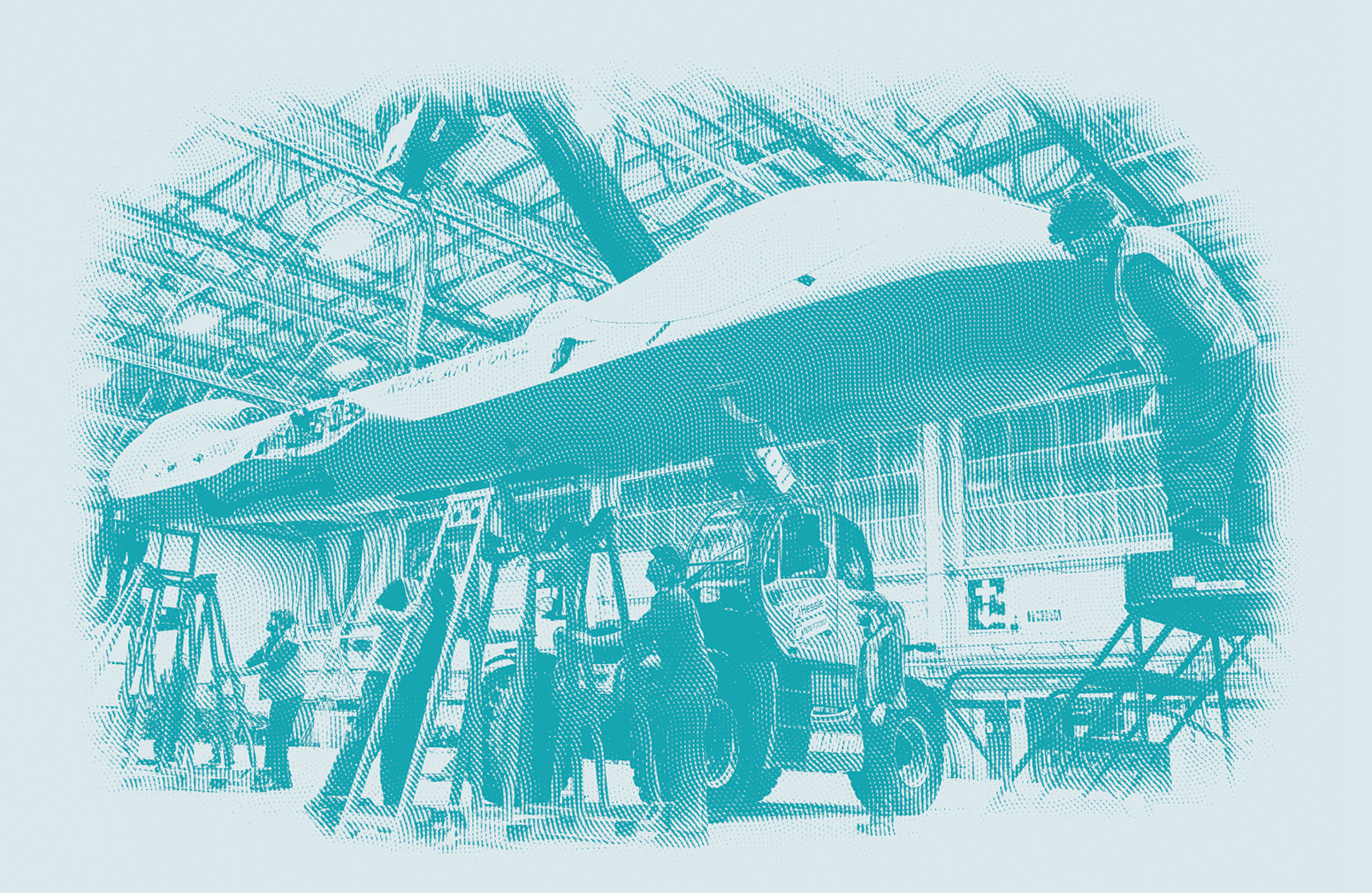
CASA is neutral about new manufacturing technologies, the regulator’s Design and Manufacturing Oversight Manager Rohan Salgado says.
‘From CASA’s perspective, any component or process used in manufacture or repair of an aircraft has to meet the applicable airworthiness requirements,’ he says. ‘That is a basic principle, whether the process used is traditional or new.’
And while the techniques of additive manufacturing can be astonishingly fast, the approvals process for additively manufactured components necessarily takes longer, to assure safety, Salgado says.
It’s important to remember acceptance of traditional methods, which now include composite manufacturing, didn’t happen overnight, he says. ‘It took a while for composite manufacturing methods, standards and compliance to be settled, but now they are established standards. Additive manufacturing will get there.’
The GE Catalyst engine that will power the new Cessna Denali aircraft has more than 30% of its components made using additive technology.
Beyond 3D printing
There are 7 additive manufacturing techniques in widespread use, and at least 22 variations on these.
Material extrusion
This is the most common additive manufacturing technique in which thermoplastic material is pushed through a heated extrusion nozzle and deposited layer by layer to build an object. Material extrusion is also known as fused filament fabrication and fused deposition modelling. This is how low-cost hobby 3D printers work, but material extrusion is also used in aerospace, automotive and medical applications, to quickly produce prototypes and parts.
Sheet lamination
Also called laminated object manufacturing, this is the joining, or laminating, of sheets of material. It is useful for building durable 3D objects with complex geometries. Materials including paper are bonded with adhesives and heat, then cut with computer numerically controlled lasers or blades to produce the 3D object.
A variant of sheet lamination is ultrasonic additive manufacturing that ultrasonically binds layers of metal sheets to metal substrate surfaces.
Binder jetting
This method uses 2 elements – a powder-based material and a liquid binder that acts as an adhesive between layers of the powder. A print head, similar to that of an ink jet printer, deposits alternating layers of build material and binding material. After each layer, the object being printed is lowered on its build platform. Binder jetting works with materials, including ceramics, composites, sand and plastics.
Material jetting
In this technique, droplets of thermoplastic are selectively deposited by a printer head and cured using an ultraviolet light source.
Directed-energy deposition
This technique uses a laser or electron beam to melt metal powder or wire. Parts are created by placing the melted material where it is needed. It is commonly used to repair or add material to existing parts.
Powder-bed fusion
This technique uses a heat source such as an electron beam or laser beam to melt and join material powder to create three-dimensional objects. Powder-bed fusion can be used to create both plastic and metal parts. The beam heats a thin (typically 0.1 mm) layer of powder, after which the build platform lowers by a corresponding amount, and the process repeats.
Variations on powder-bed fusion include direct metal laser sintering, selective laser sintering – which compact the material without melting it – and selective laser melting. Electron beam melting is used for metals but requires a vacuum for the beam to operate.
Vat photopolymerisation
A vat or container filled with photosensitive liquid resin is exposed to a light source to create solid objects. It is in some ways analogous to a 3D photographic print. The build platform lowers from the top of the tank as, layer by layer, an ultraviolet light source selectively cures the liquid resin to produce the object. When finished, the object is submerged in a chemical bath that washes away excess resin, and cured in a UV oven to increase its stability and strength. Forms of vat photopolymerisation include stereolithography, digital light processing and continuous liquid interface printing.