A helicopter incident is a reminder of the ever-present hazards of bearing deterioration and metal fatigue. If not for sheer luck, the headline here would have been 4 failures and a funeral.
Bell 206L-3 Longranger 60 km south-west of Deniliquin, NSW Wednesday 9 December 2022.
The first sign of trouble was unequivocal: a loud ‘bang’ from above and behind the pilot. The helicopter pitched nose up, rolled left and began to vibrate severely. The flight was surveying a forest in western NSW less than 30 feet above the treetops, meaning there was no near place to land.
The pilot moved the cyclic to counter the pitch and roll and flew straight for about 10 seconds, when suddenly the vibration stopped. The pilot made a quick assessment that the helicopter was still flying well and flew a slow turn to reach farmland about 2 kilometres away.
Those few seconds must have seemed to pass agonisingly slowly. The pilot made a precautionary landing on open land, without further damage to the helicopter or injury to the 3 people on board.
An inspection found the right, forward, pylon support link assembly had fractured. This assembly forms part of the nodal beam transmission suspension system, that isolates and supports the main rotor transmission and rotor, and reduces cabin noise and vibration to tolerable levels. The link is an alloy forging with an X cross-section on its shaft and an eye at each end, like an oversized ring spanner. Within these eyes are simple bearings surrounded by shims and cushioned by rubber-like elastomeric material.
Many fixed-wing aircraft use elastomeric materials as part of their engine mounts. Most of these, like the elastomeric bearings used in the incident helicopter, are made by the Lord Corporation (now part of the Parker Aerospace conglomerate), which has made isolating mounts of one sort or another since 1924.
The link had failed from metal fatigue (see sidebar on next page) but this had been caused, at least in part, by the deterioration of the elastomeric material surrounding the bearing at one end. As the elastomer deteriorated, it lost its ability to absorb the vibration of the helicopter transmission, and this had been passed through to the link, shaking it until it broke.
From the Australian Transport Safety Bureau (ATSB) report:
- Bell concluded that the shim fretting damage and wear, and deterioration of the elastomer was consistent with bearing degradation during service and that, as the bearing degraded, loads in the link would have increased.
The ATSB found the Longranger’s airframe had accumulated 8,054 hours over 39 years of operation in the US and Australia. The link had been installed in July 2003 at 3,507 airframe hours. It was an overhauled item, regarded as having zero hours.
The ATSB laboratory found no manufacturing defects and the manufacturer verified it was a genuine component. There was no record of the link assembly having been overhauled since its original installation, meaning it had 4,547 hours in service at the time of the occurrence. Lord’s general advice on elastomeric bearings was they were designed for long life and had ‘gradual’ modes of degradation.
Enquiries with the helicopter’s maker Bell turned up 3 other two-link assembly fractures in helicopters. Two were in the same right, front location and fractured in approximately the same place as the link on the Australian helicopter.
From the ATSB report:
- The first occurrence involved a hover-taxi at an airport at 20–50 feet above the ground. A large ‘crack’ sound was heard, after which the pilot was unable to maintain level flight. A hover-autorotation was attempted and resulted in a hard landing. The pilot and passengers were uninjured.
- The second occurrence happened during a sightseeing flight at around 900 feet. A large ‘bang’ was followed by an uncommanded left bank. The pilot attempted to compensate with control inputs, but was unable to maintain both altitude and direction. The pilot attempted a ditching but upon flaring the helicopter, it rolled left and impacted the water. All occupants were able to escape and swim to shore.
- There was one case in 2008 of a left rear link assembly fracture, which resulted in a precautionary autorotation landing.
The accidents highlighted the lucky break that saved the pilot and survey crew on the Australian helicopter, who had neither altitude nor a suitable landing area nearby. The fractured ends of the link had become fouled on each other; this had stopped the airframe vibration and given the pilot a semblance of control that lasted until landing.
RTFM
Of the myriad acronyms in aviation, RTFM is among the most profound in its safety implications, particularly concerning maintenance. It stands for ‘Read the manual’, with a vulgar word added to emphasise the fundamental importance of doing so. The point is that delicate sensibilities are acceptable collateral damage, so long as this message – R-T-F-M!!! – is received and understood.
In the polite words of the ATSB report
However, the helicopter maintainer had not been removing the link assemblies in accordance with the helicopter manufacturer’s maintenance manual inspection requirements. This reduced the likelihood of detection of the degraded bearing.
The most recent airframe inspection had been on 8 November 2022, one month, but only 12 flight hours, before the occurrence. Inspection of the link assemblies had been done without them being removed from the helicopter. No defect was recorded.
Chapter 63 of the Bell 206L3 Maintenance Manual says, ‘Inspection of elastomeric bearings is feasible only with the link assembly removed from the helicopter.’ But the helicopter’s maintenance organisation told the ATSB it had not been aware of the need to remove the links.
Its procedure was to examine them in situ for evidence of ‘dust’ or ‘crumbs’ that would indicate deterioration of the elastomers. The links had been removed from the helicopter during inspection of the main transmission, 587 hours before the failure and probably inspected then.
There was a further barrier to detecting elastomeric degradation: a varnish-like coating had been applied to the elastomers to protect against oil contamination. This had had the effect of trapping the dust and crumbs of deterioration, making them more difficult to see. Lord Corporation advised it had not applied this coating. This procedure was included in the maintenance manual, which cautioned the coating thickness should not prevent inspection of the component for deterioration. But the maintainer told the ATSB it would abandon sealing elastomeric bearings as one of the lessons it was determined to learn from the incident, along with removing the link assemblies for detailed examination, in accordance with the maintenance manual.
Once a fatigue crack begins, it grows every time the load is applied – slowly at first, then very fast.
Elastomeric bearings removal criteria: Lord’s commandments
In every case in which removal criteria exist in a maintenance manual, these should be followed. However, when the elastomeric bearing is not covered by a maintenance manual, the following general guidelines may be used:
- If the bearing is visibly degraded to such a degree that it allows excessive motion or vibration, remove and replace it.
- If the bearing has visible compression set and it appears this will lead to difficulty in installation or increased vibration, remove and replace it.
- If enough elastomer has been extruded to allow the shims to touch or if there are any cracked shims, remove and replace the bearing.
- If the bearing is separated (due to fatigue or bond line damage) over more than 25% of the bonded area, remove and replace it.
- If the bearing is ‘oil’ contaminated to a slight degree, it should be cleaned with a water-based detergent, rinsed and dried. If the contamination damage is extensive, removal and replacement are required.
- If the bearing exhibits a very unusual damage condition, it should be returned to the maker for further analysis.
The best removal criteria are always based on the maintenance manual and experience. However, when in doubt, take it out!
Source: Lord Corporation white paper, Elastomeric Bearing, Dampers and Isolators: ‘Comfort, care and feeding’. Revision 2, 2006
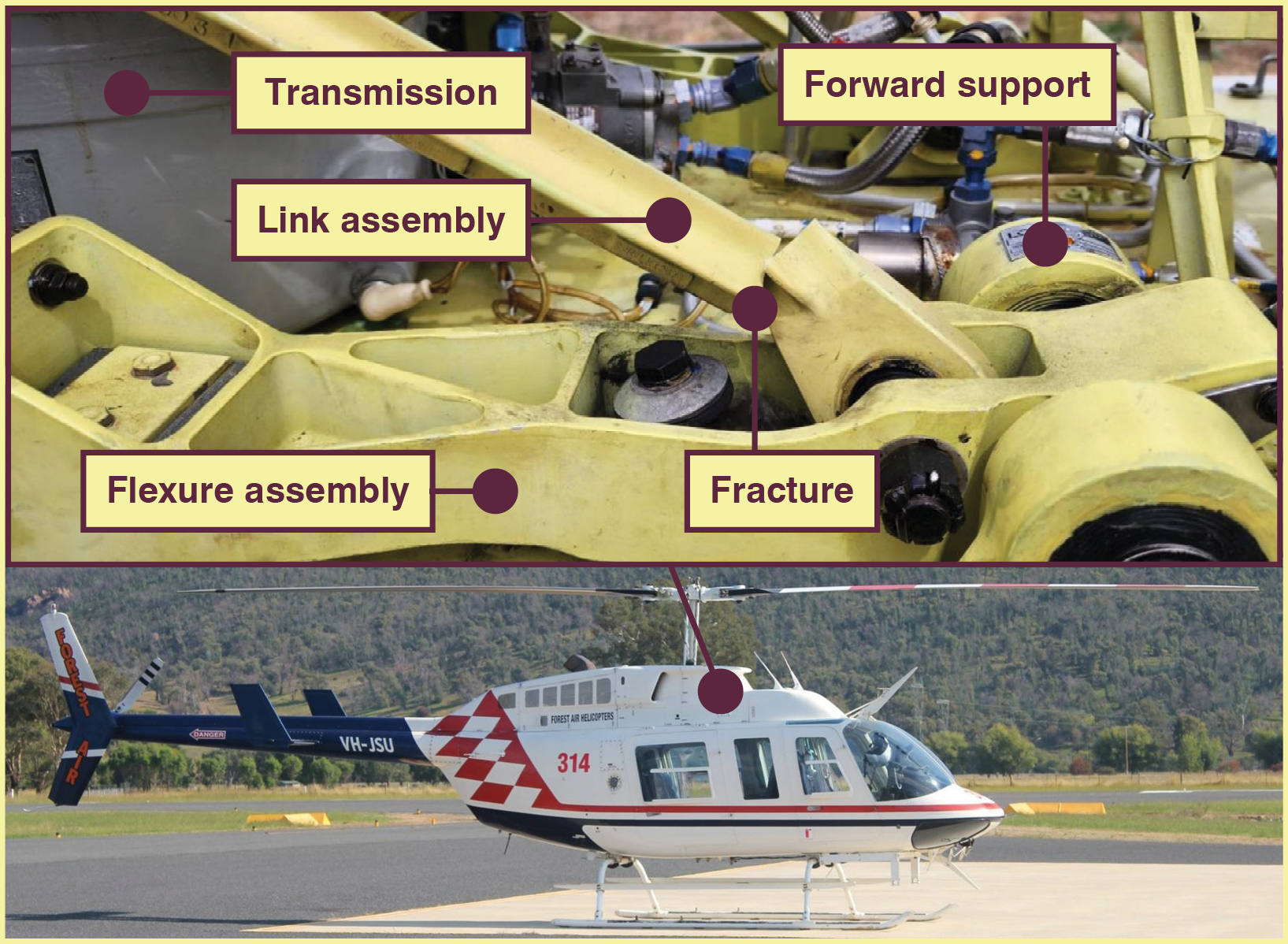
Metal fatigue
Metal fatigue, defined as the initiation and propagation of cracks in a metal component or structure due to repeated loading, is the enemy of all metal aircraft. Once a fatigue crack begins, it grows every time the load is applied – slowly at first, then very fast. This can often be seen in the cross-section of a failed part; a series of marks like tree growth rings give way to a sudden instantaneous fracture. The frightening thing is, before failure there is no easy way to tell the difference between 2 identical parts that have been subjected to differing fatigue environments, except by analysis under an electron microscope.
Fatigue is a particular foe to helicopters. A 2013 study by AgustaWestland covering 30 years of its helicopter operations found fatigue accounts for approximately 55% of all failures in helicopter components.
CASA Airworthiness Bulletin 2-015 of 2006 remains a thorough and sobering guide to metal fatigue in helicopters. It says fatigue becomes especially significant if a helicopter is operated outside what would be considered by the manufacturer (and specified in the Type Certificate) as the operations for which the helicopter was designed and certified.
Examples of situations where fatigue lives may be affected are:
- Operation of helicopters in low-level flying, agricultural, mustering or other operations where high loads may be encountered more frequently than envisaged by the designer/manufacturer.
- Operations where there are a high number of landings and take-offs per operating hour.
- Where there is history of design or flight manual limitations being exceeded, even if only for a short time and on an infrequent basis. A single exceedance is enough to cause damage that may potentially lower the fatigue life of a component.
- Frequent operations at or near maximum all-up weight. Fatigue damage may be caused to components and not be apparent during any routine inspections. The component may still be capable of taking limit loads, but may fail unexpectedly at a lower life than published. In many cases, there will be no warning of an impending fatigue failure, as progression from a small flaw to final fracture can be very fast.
The bulletin recommends all operators and maintainers keep a detailed record of the operational history, beyond recording hours and cycles. The things to record include:
- Times, dates and durations of any flight manual limit exceedances, no matter how transient – even if they occur only once. The manufacturer should be consulted for advice if a transient overstress or flight limit exceedance occurs.
- Times, dates and durations of unusual operations, for example – a helicopter goes from being a private helicopter used for personal transport to an agricultural or mustering machine. This change in operations needs to be managed and the risk properly assessed. The manufacturer should be contacted for advice on how the change in operations affects component fatigue lives.
- Times, dates and circumstances of changes in the helicopter’s operational environment i.e. long period of storage in hot, humid, salty environments or storage in dry, dusty environments. Long periods of storage in an aggressive environment can sometimes lead to increased corrosion, which can worsen or initiate fatigue cracking.
- Operators of aircraft where more than 4 rotor full stops per hour are achieved should consult the manufacturer giving full details, including previous history of all operations, for possible life revision.
Learn more about the effects of fatigue on life limited components in CASA Airworthiness Bulletin 2-015.