It seemed like a good idea at the time, and it saved 200 labour hours, but it turned out to be a human factors and safety culture debacle that led to the deaths of 273 people.
On Friday 25 May 1979, Captain Walter Lux and First Officer James Dillard lined up a McDonnell Douglas DC-10 on runway 32R at Chicago O’Hare Airport for a trip to Los Angeles. Take-off was unremarkable until rotation, when Dillard said ‘Damn!’ just before the cockpit voice recorder cut out.
The reason for his mild outburst was obvious to the tower and, in all likelihood, to some of the passengers on the left side of the aircraft. The No 1 engine and pylon had detached from the wing and fallen backwards over it. As the accident was after V1, the take-off decision speed, the crew had no choice except to continue the take-off.
A maintenance supervisor had been waiting to cross the runway in a vehicle and had a close view of the event. He told investigators of seeing the No 1 engine ‘bouncing up and down quite a bit’ and detaching, climbing and flipping back over the wing
The supervisor saw the aircraft make a ‘fairly normal climb’ and presumed it would return to the airport.
But after the DC-10 had reached about 300 feet, it began a left roll and bank that the flight data recorder later disclosed reached 112 degrees, combined with a 21-degree nose-down pitch. It crashed into a field 1,400 metres north-west of the airport, killing all 271 on board and 2 people on the ground, in a fireball fuelled by the 79 tonnes of jet fuel onboard.
Suspicion
The loss of an engine should not have caused the crash: the DC-10 was certified to be able to take off at maximum gross weight on 2 engines. The first clue to what had gone wrong came from the engine that fell on the runway.
Investigators found a thrust link bolt, which was initially suspected of contributing to the crash through fatigue failure. But it was exonerated when its failure was found to have been through overload, not fatigue. A breakthrough came when a dent in the rear pylon bulkhead was found to match the shape of the wing fitting to which it was normally bolted. This suggested maintenance-induced damage.
Improvisation
National Transportation Safety Board (NTSB) inspectors went to the American Airlines maintenance facility in Tulsa, Oklahoma, and were taken aback to see how engineers changed DC-10 engines. The airline had written an engineering change order (ECO) that saved about 200 labour hours per engine and had a potential safety benefit in reducing the number of systems that had to be disconnected and reconnected from 79 to 27.
McDonnell Douglas had recommended the engine be removed separately to the pylon holding it, but the ECO involved removing the entire engine/pylon combination, using a forklift with an engine shipping stand on its tines to support their combined weight. Other airlines had been using a similar procedure, and the investigation found 88 of the 175 recorded engine and pylon removals by US DC-10 operators had used this method or variations, such as using a crane.
A McDonnell Douglas field inspector knew of this process and had recommended against it, saying, ‘Douglas would not encourage this procedure due to the element of risk’, but the company had no legal power to prohibit it. No McDonnell Douglas employee ever saw the removal and replacement processes being performed.
It’s important to say clearly that the maintenance crews were not gleefully doing the wrong thing so they could save time – they thought they were doing the right thing. The combined centre of gravity for the engine and pylon combination had been calculated for the procedure and the forklift placed under this point as precisely as possible. The procedure had been analysed, but some of its associated risks had escaped consideration. The result was that scheduled passenger flights became test flights for the new procedure.
Later investigation found a skilled operator could move the forklift with a finesse of 4–5 mm, but that the forklift used on the doomed aircraft had a faulty hydraulic valve that meant it dropped by 25 mm in 30 minutes while switched off, as had happened during the shift change on the job. The sagging forklift had stressed the rear pylon bulkhead.
Airworthiness directive inspections found 8 aircraft had overload cracks in the same area of the pylon that was damaged on the accident aircraft. One DC-10 had an engine that engineers could rock back and forth by hand.
The investigation also uncovered widespread shortcomings in engineering safety culture, incident analysis and reporting. Continental Airlines had cracked the rear pylon bulkhead on 2 of its DC-10s during maintenance in late 1978 and early 1979, with one of these incidents having been described as sounding like a pistol shot. Continental had also worked out that a faulty forklift was implicated in the two incidents and repaired it. But the first the Federal Aviation Administration heard about these close calls was after the Chicago disaster.
Consequences
The question of why the DC-10 had crashed despite having sufficient power to fly was explained by the collateral damage that came when the engine fell off. As it departed, it ripped out lines from the No.1 hydraulic system that controlled the leading-edge slats on the left wing and locked them in place, causing the left outboard slats to retract under air pressure – the right-side slats stayed deployed. Slat retraction raised the stall speed of the left wing to about 159 knots, 6 knots higher than the take-off minimum airspeed (V2) of 153 knots, and put the aircraft into a state of asymmetric lift
The engine also ripped out the No 1 electrical bus and several systems and instruments immediately lost power. Among these were the captain’s flight instruments, the left-wing stall warning, the stick shaker and the slat disagree warning light system. The flight crew were therefore unaware of the lift asymmetry between the wings and had no stall alarm or stick shaker to warn them.
Conclusions
By a tragic irony, the pilot flying had throttled back to V2, which brought about the stall that sent the aircraft into the ground. The pilot had followed procedures to the letter and was probably not aware that the engine was no longer attached to the wing. Multiple factors doomed all the people on the aircraft: drift from established procedures, lack of communication and maker’s advice ignored. It’s a horror story that all aircraft maintainers should know and seek never to repeat.
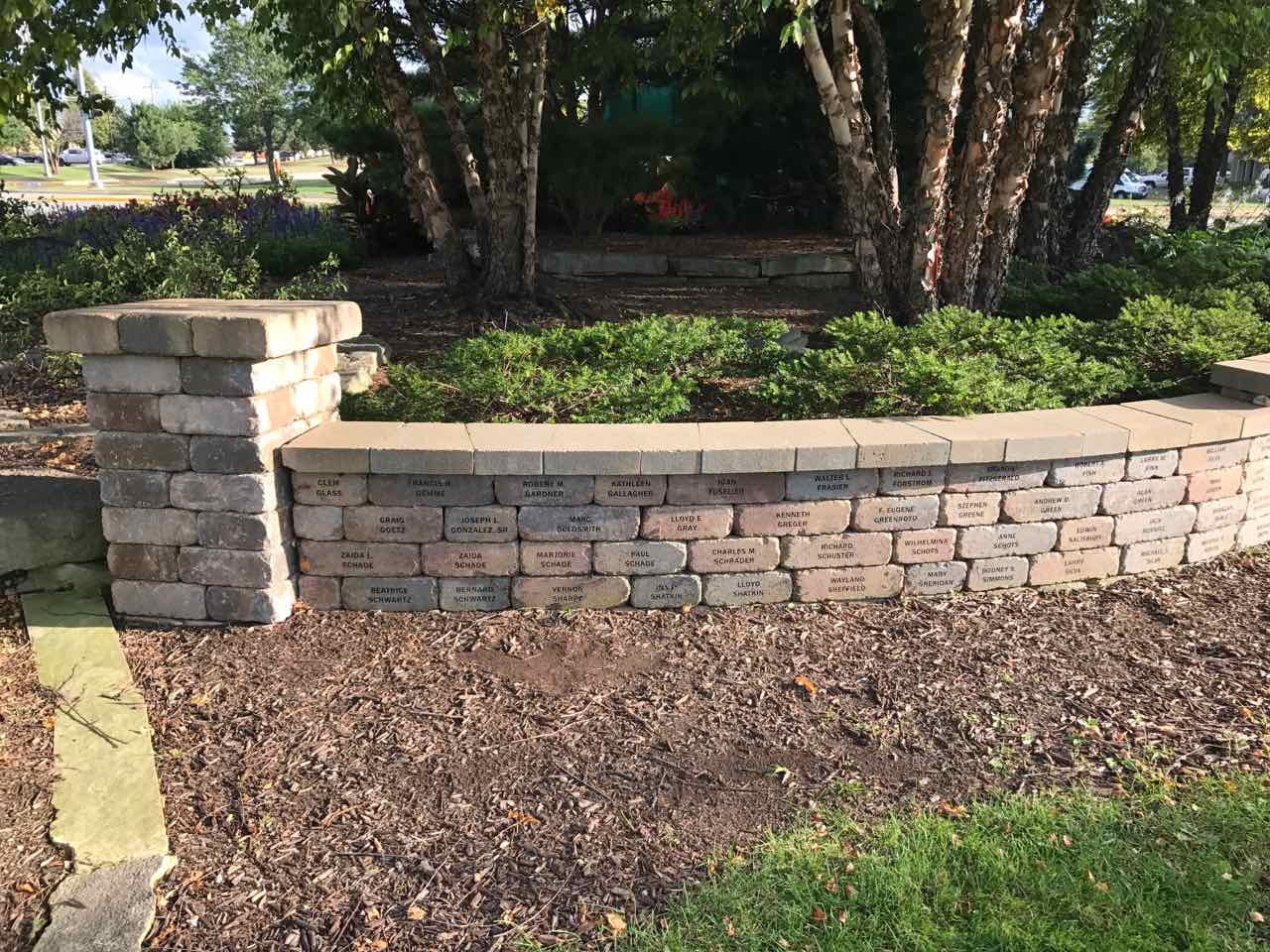