The lessons learnt from the series of small failures that led to an airliner full of passengers taking off with its pitot covers still in place apply equally to general, recreational and unmanned aviation.
Brisbane airport hosts 31 airlines, a Royal Flying Doctor Service base and one distinctive species of insect. The keyhole wasp (Pachodynerus nasidens), an exotic species originally from South America, makes its only Australian home at the airport.
By an evolutionary fluke, these insects find aircraft pitot tubes irresistible as places to build nests and store their prey of paralysed flies and spiders. This is probably due to the tubes’ resemblance to the abandoned insect nests the wasps habitually commandeer as homes.
Because pitot tubes are used to measure airspeed, blockage by wasp nests is a serious hazard and has been implicated in 2 incidents of unreliable airspeed indications in aircraft taking off from Brisbane. Similarly, in 1996, Birgenair flight 301, a Boeing 757, crashed soon after take-off from the Dominican Republic, killing 189 people. This was attributed to a nest-building wasp (although the wasp was a different species).
Australia has at least 10 native species of wasps, colloquially known as mud, dauber or potter wasps, but none of these appear to have the same predilection for setting up home in aircraft pitot-static systems.
Commercial aviation is a business of managing hazards and, for ground handlers and aircrew at Brisbane, Pachodynerus nasidens is just another item on a long list of hazards. Excluding the wasp requires covering pitot tubes while an aircraft is on the ground. Brisbane is one of only a few airports in the world where this practice is recommended, even for short aircraft turnarounds. Wasps have been seen in pitot tubes within minutes of an aircraft landing.
These covers, like control locks, are attached to long, prominent tags, bearing 3 words that are a catchphrase for thoroughness and high seriousness in professional aviation operations: remove before flight.
But if thoroughness and high seriousness are absent, the mitigation becomes a hazard in itself. This happened in Brisbane on the night of 18 July 2018 when Malaysia Airlines flight MH134 took off with all 3 pitot tube covers still in place. Although nobody was hurt in the incident, the Australian Transport Safety Bureau (ATSB) was sufficiently concerned by the potential for a similar disaster to the Birgenair crash to publish a long and detailed report. It paints a disturbing picture of confused responsibilities, blocked information flows and an insidious pattern of deviance from standards and practices.
Confusion and drift
The ATSB found the covers had gone undetected despite 4 walk-around inspections of the aircraft being required between them being fitted and the aircraft taking off. Two of these inspections were not done.
Surveillance video showed the flight crew walkaround had been a quick and cursory stroll, with light from the captain’s torch shining briefly on the pitot covers, but the captain not registering their presence. The ATSB said this literal oversight may have been related to the absence of any mention in the airport information used by the crew of Brisbane’s wasp problem and need for pitot protection. Confusion over who performed what duties between 2 engineers meant the engineering pre-departure walkaround did not take place and a similar confusion between 2 members of the dispatch crew meant the final walkround, the pre-dispatch inspection, also never happened.
From the ATSB report:
The procedures specifically included checks of the pitot probes and should have presented multiple opportunities for the covers to be detected and removed, in addition to incidental opportunities during general ground activities. In each case, individual errors and violations prevented the detection and removal of the pitot probe covers.
[The report] paints a disturbing picture of confused responsibilities, blocked information flows and an insidious pattern of deviance from standards and practices.
But the report also put these errors and violations in context. Some engineers at the aircraft’s Brisbane-based maintenance services provider used pitot probe covers even when operators did not explicitly require it. Malaysia Airlines was one such operator. The ATSB noted this increased the likelihood of error associated with the use of pitot probe covers because the provider’s engineers were not permitted to make technical log entries.
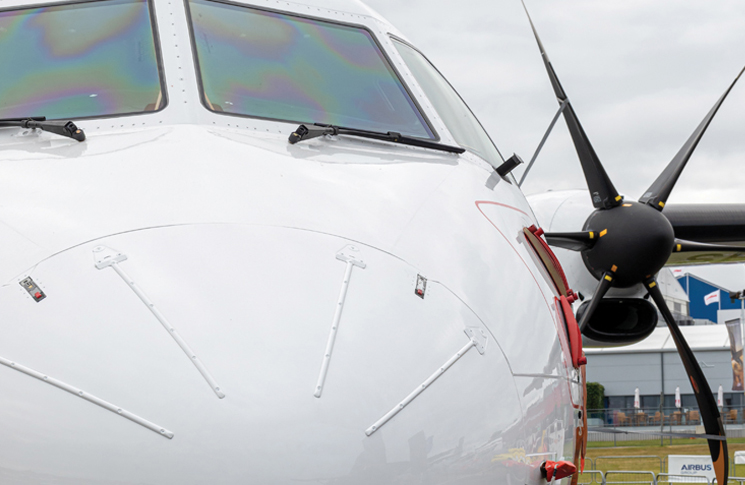
The Malaysia Airlines’ engineer who travelled with the aircraft did not routinely use pitot probe covers, and never used them during turnarounds. The ATSB noted the research of Swiss cheese theory pioneer James Reason and US aviation psychologist Key Dismukes about the extreme difficulty of reliable prospective memory – the act of ‘remembering to remember’ when there are no reminders. The streamers on the covers were not particularly large.
During take-off, the aircraft’s primary instrument displays showed red speed flags in place of airspeed indications from early in the take off roll but for unexplained reasons the flight crew did not respond in time for the take-off to be safely aborted.
Once airborne they declared pan pan, but the tower controller did not respond, ‘for reasons that are unable to be determined’. The crew climbed the aircraft to 11,000 feet and began troubleshooting the problem. As part of this, they shut down the aircraft’s air data systems, which activated the backup speed scale (BUSS), a software-based system which derives a safe airspeed range (represented on the display by a green band in place of a speed figure) from angle-of-attack and engine thrust data. Not all A330s have the BUSS, which is an expensive option, but this one did, and the crew were trained to use it.
The incident’s final indignity was damage to the landing gear doors caused by an emergency gravity deployment of the gear – this was made necessary by the lack of air data.
The ATSB’s analysis went beyond the errors and omissions made by individuals on the night. It found systems to identify hazards and ensure these were being mitigated were either absent or had not worked. Knowledge of Brisbane’s wasp issue had reached some parts of Malaysia Airlines, but not others, for example.
Sting in the tail
The short flight of MH134 can be analysed from many standpoints: drift into failure, normalisation of deviance and a case of the holes lining up in an unusually large number of conceptual Swiss cheese defensive layers, are only 3 of the possible angles. For managers it is a cautionary tale about making sure work as imagined lines up with work as done.
Those lower down the workforce food chain (or flying for themselves) have ATSB Chief Commissioner Angus Mitchell’s words for (limited) comfort: ‘It’s important to treat every safety-related task or inspection as though it could be the last barrier to protect against an accident,’ he said.
Indeed it is, but individual diligence is a delicate flower that withers quickly without consistent support from management. The responsibility is everyone’s. It takes an entire organisation to defend against a determined wasp.
For more information on managing wasps, see Airworthiness Bulletin, AWB 02-052, ‘Wasp nest infestation – alert’. |
Maybe they should put one of those covers on the pilots control panel as well when they install them
During the 1990s I made regular light aircraft flights to a mine site at Ulan (north of Mudgee) NSW. Some of these were on the ground for a short time and I soon learned that a local hazard was a particular wasp that took a liking to pitot tubes no matter how brief the stop. I have not encountered this wasp elsewhere but have since made a point of always “covering up”.
Being involved in an investigation into an identical incident in 2013 Etihad A330 incident and air turn back it is concerning that this issue is not rammed down the throat of every operator and line maintenance organisation on a regular basis. Controlling risks to ALARP/SFAIRP includes assessing what you know and what you aught reasonably know. Ample opportunity for lessons learned and to know the hazards and control associated risks.